Technologies
Maximizing Value Through Advanced Proven Technologies
The subsequent announcement to the National Biofuel Policy 2018 permits the diversion of B-heavy molasses, sugarcane juice/syrup and sugar to produce ethanol in addition to C-molasses. This multi-feed stock option open ups various avenues to maximise value for ethanol producers.
Praj has supplied technology and plants based on various sugary streams around the globe which are successfully being operated over the past two decades.
The combination of right feedstock based on maximization of yields, overall steam and powerbalance, optimum utilization of water, chemicals and effluent treatment / ZLD technologies through right selection of technology is the key to achieve maximum benefits from existing assets.
Praj's advanced customised technology solutions that insulates industry from various challenges, are the result of its innovative and customer centric approach towards sustainable ethanol production.
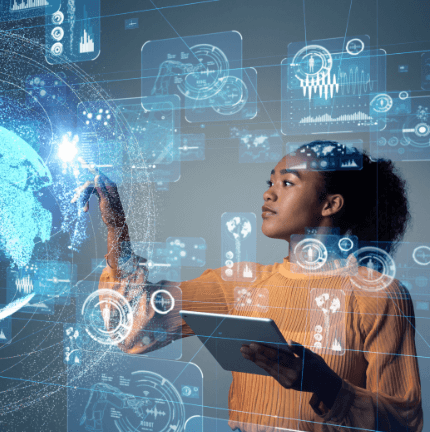
Challenges in Sugar Industry | Solutions from Praj |
---|---|
|
BIOSYRUP® technology is a unique solution to store cane juice syrup, enabling the distillery to operate around the year without depending on external feedstock. |
|
Multi feed multi product technologies without affecting effluent discharge and offering product flexibility. |
|
Praj's revolutionary PROFIIT TM (Process Optimised Flexible Integrated Incineration Technology) reduces supplementary fuel requirement by up to 60%, leading to lowest operating cost for incineration and reducing plant carbon foot print. |
|
EcoCoolTM technology conserves water by reducing its consumption upto 75% as a better alternative to conventional cooling towers. |
|
MAXIMOLTM technology is an innovative bed booster technology to increase production capacity of existing MSDH plants up to 30% without increasing plant footprint. |
|
BIOSYRUP® technology helps to achieve upto 50% production capacity enhancement by diverting excess sugar. RenGasTM technology generates additional revenue by converting mill waste press mud to compressed bio gas. |
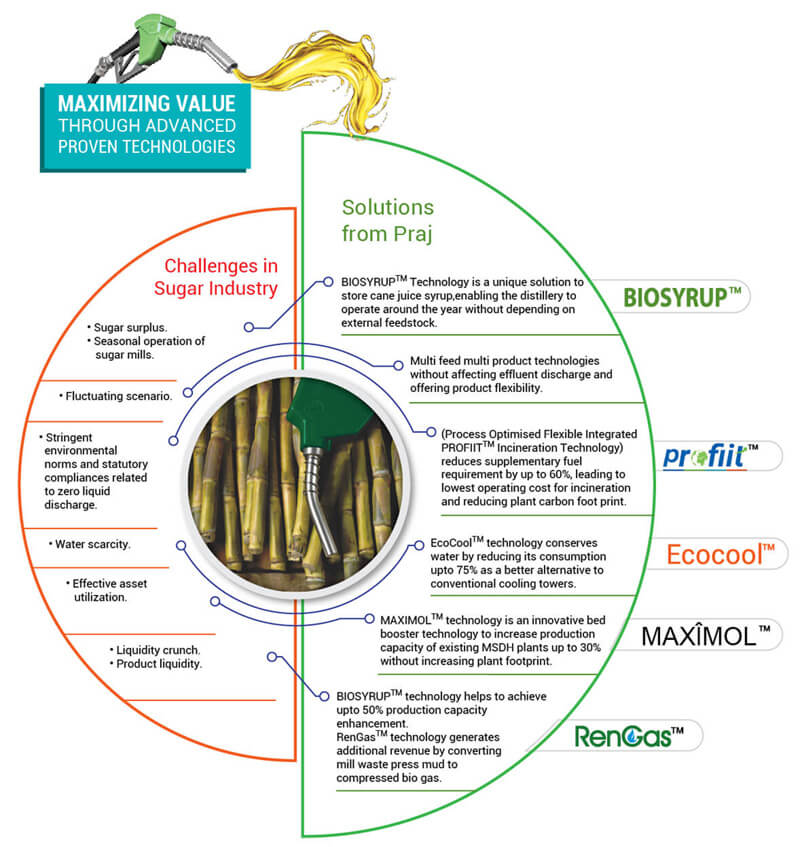
BIOSYRUP® for reliable, round-the-year ethanol production
Praj has more than 15 years of experience in converting various sugar streams like diluted/ mixed juice/ syrup, sugar or B-heavy molasses into ethanol in a sustainable and profitable manner. By harnessing its BIOSYRUP® technology to store diluted sugar streams, Praj has helped the industry solve the problem of round the-year availability of feedstock. This also helps the industry cope with market pressure despite a volatile and uncertain environment.
Some of the challenges in handling sugarcane juice / syrup as feedstock are -
- Results of conversion vary fro factory to factory.
- Since sugar mills operate seasonally in 3-5 month cycles, storage can result in loss of sugar due to bio degradation
- Possibility of bacterial contamination during fermentation could leadto loss of production yield and efficiency.
- High operating cost for low solid spent wash treatment when using B-heavy molasses.
Some of the challenges in handling sugarcane juice / syrup as feedstock are -
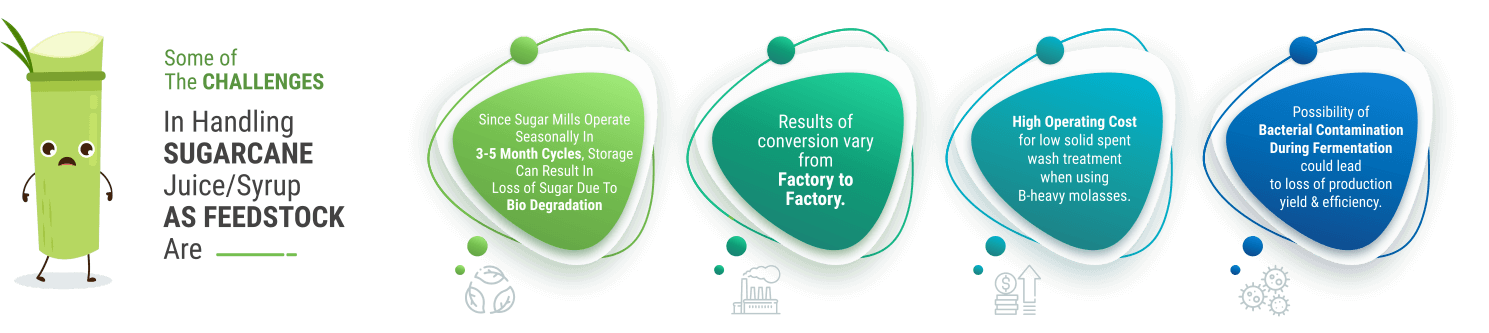
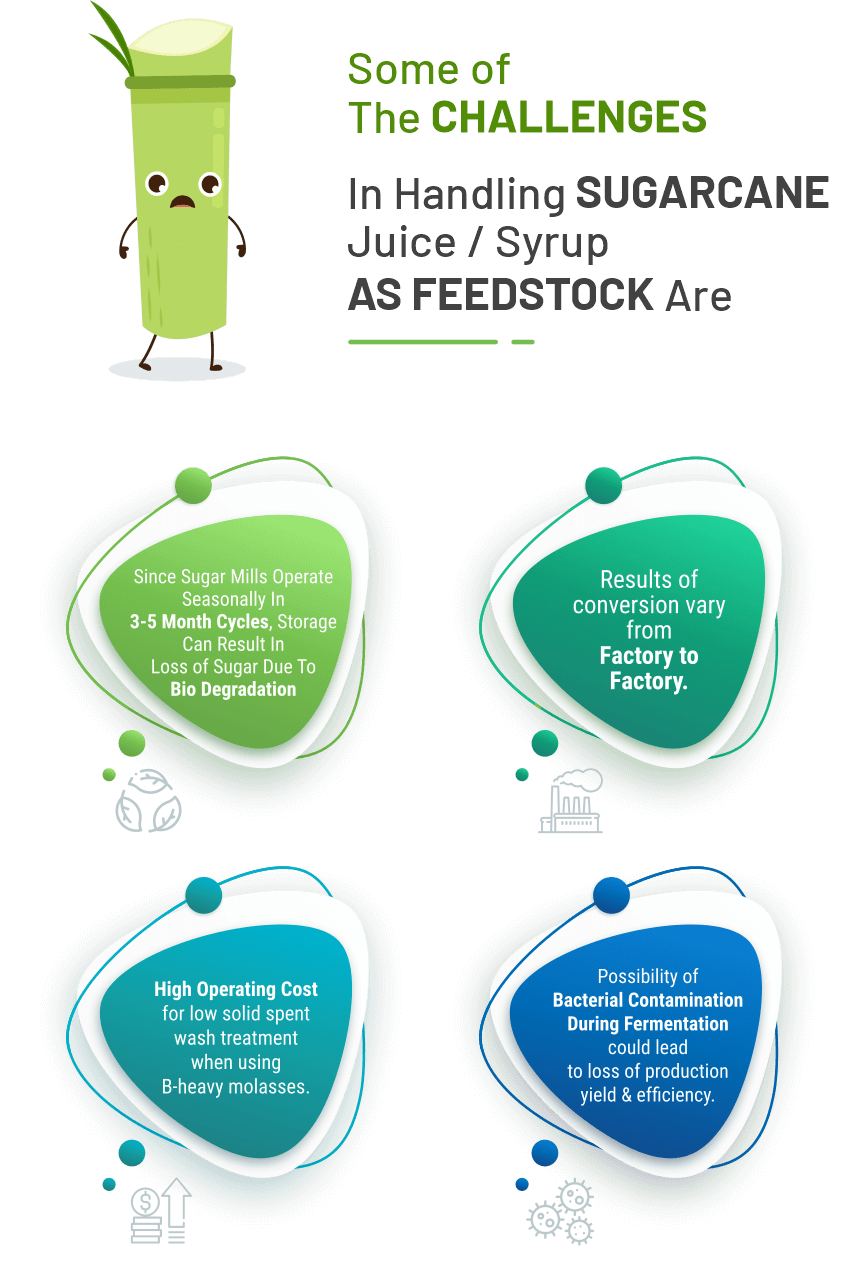
Praj has set up plants across the globe ranging from 60 KLPD to 600 KLPD using independent sugar streams or in combination with each other. Benefits of Praj's BIOSYRUP® technology include
- 1) Easy storage of concentrated sugar cane juice/syrup for year-round operation.
- 2) Zero bacterial contamination for reliable operation.
- 3) Higher production yields.
- 4) Reduced volume of effluent resulting in lower operating cost, without affecting production yield and efficiency.
- 5) Improvement in overall production yield by 0.5% in sugarcane juice and B-heavy molasses as compared with C-molasses.
- 6) Lower OPEX.
- 7) Zero liquid discharge (ZLD) system
Round the year operation with BIOSYRUP®
Power of Seven in Colombia
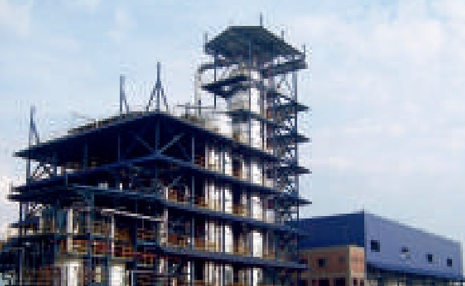
Incauca S.A. (300 KLPD)
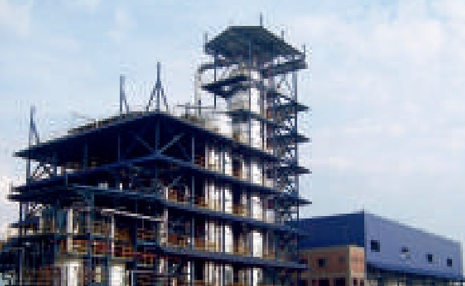
Incauca S.A. (400 KLPD)
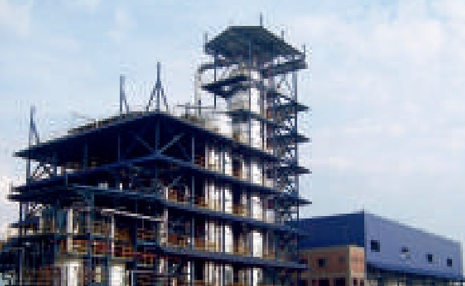
Incauca S.A. (500 KLPD)
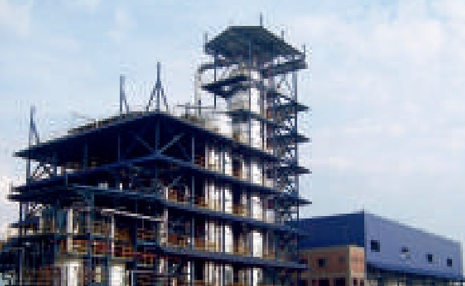
Incauca S.A. (600 KLPD)
Praj has set up plants across the globe ranging from 60 KLPD to 600 KLPD using independent sugar streams or in combination with each other. Benefits of Praj's BIOSYRUP® technology include
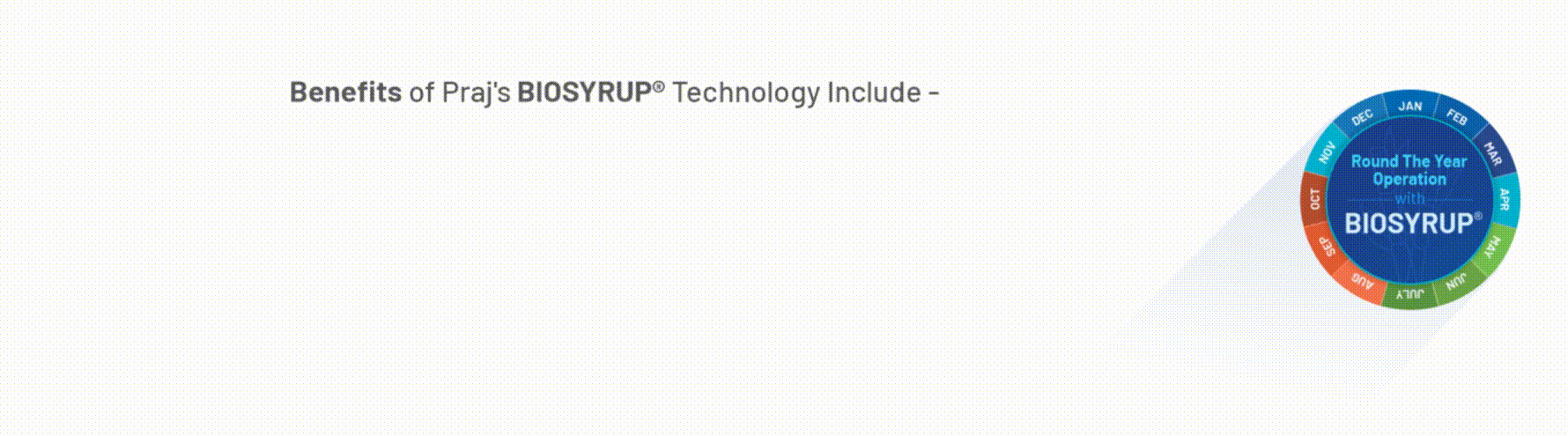
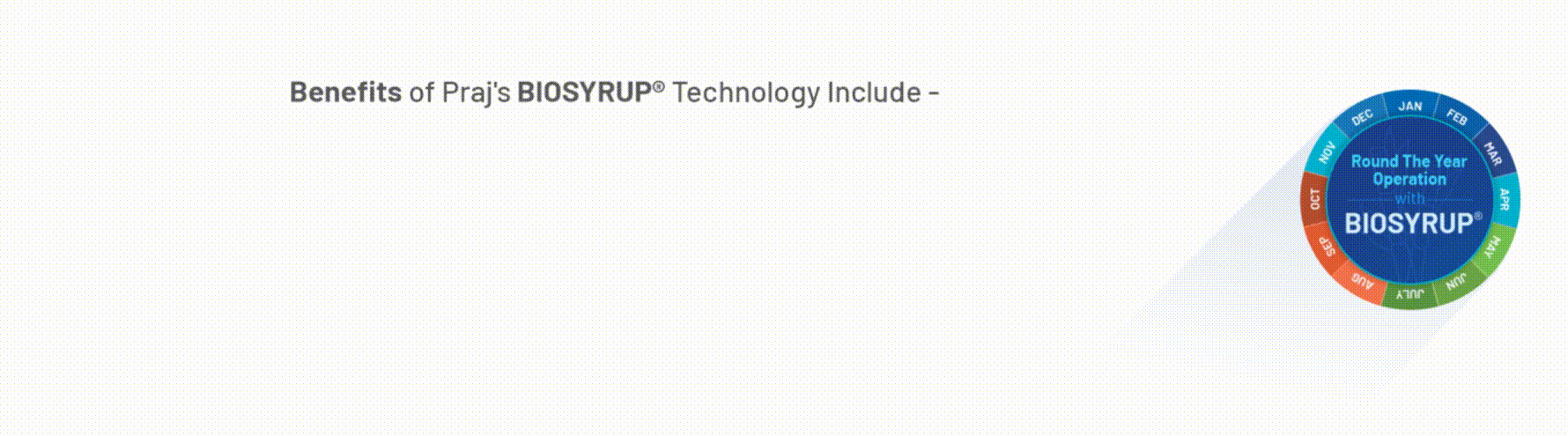
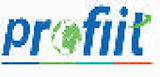
Incineration technology with lowest OPEX
Process Optimized Flexible Integrated Incineration Technology (PROFIITTM) helps distilleries create sustainable processes and makes their business more profitable. This technology is the result of Praj’s extensive research in integrating processes with incineration technology, in partnership with Thermax Ltd. PROFIITTM helps customers to not only tackle the problem of waste generated during process but also helps their business achieve sustainable profitable growth. Spent wash in distilleries are currently incinerated in boilers which impact operational efficiency and profitability. It consumes supporting fuel, involves high OPEX, has low efficiency and generates high ash which cannot be easily disposed. PROFIITTM overcomes these problems, with additional advantages such as-
-
1. Reduction in support fuel for incineration boiler.
Fuel Conventional incineration boiler technology PROFIITTM incineration technology Savings with PROFIITTM incineration technology Coal 80-85 TPD 24-25 TPD 56-60 TPD Bagasse 120-140 TPD 40-45TPD 80-95 TPD Rice Husk 90-95 TPD 28-30 TPD 62-65 TPD up to 60% reduction in supplementary fuel
-
2. Reduction in overall water consumption for distillery complex to 1-1.2 lit/lit of alcohol.
-
3. High quality ash generation.
-
4. Additional yield of up to 2-3 lit per ton of molasses.
-
5. Reduction in steam consumption by 15-20% making the distillery self-sufficient for steam and power.
-
6. Reduced OPEX due to reduction in CIP chemicals, acid, and cost of chemicals in process condensate treatment plant.
-
7. Reduced CAPEX due to low civil cost in fermentation, evaporation and process condensate treatment plant.
EcoCoolTM Water conservation for distilleries
Evaporative cooling towers are conventionally used in distilleries which result in loss of water.
Praj has successfully installed air cooled heat exchangers (ACHE) at Swaraj India Agro Ltd., to help conserve 6 litres fresh water per litre of alcohol produced.
EcoCoolTM drastically reduces water consumption up to 75% as well as cost of pre and post treatment of water.
Through process integration, this tool can be leveraged in brown field and green field distillery plants, and adapted to any ambient and humid conditions across the world.
Advantages
- Consumes lesser soft water since there is zero evaporation and drift losses, and therefore does not require makeup water.
- Lower operational expenditure (OPEX).
- No blow down of water ensures recirculation of water quality and water conservation.
- Saving in soft water reduces cost of procurement and treating raw water.
- Reduces OPEX for maintenance of cooling towers and scaling in heat exchanger tubes.
- Reduces cost of treating blow down water.
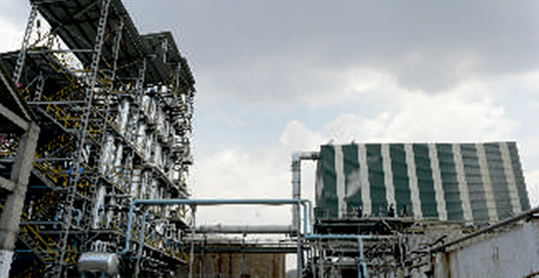
Save water up to 75% with EcoCoolTM
MAXÎMOLTM: Increasing capacity of ethanol dehydration plants by 30%
Praj introduced MaxImolTM, a dehydration technology which increases the capacity of existing molecular sieve dehydration technology. Based on EcomolTM technology, MaxImolTM provides upgraded features without additional CAPEX. The innovatively designed bed booster enhances the adsorption capacity of MSDH, thereby improving performance by 30%.
Highlights of technology
- Operator friendly interphase to swiftly switch between existing Ecomol to MaxImolTM mode and vice-versa.
- Lower operational expenditure (OPEX).
- Quick and easy installation enabling immediate turnaround.
- More than 50% of supplied energy can be recovered within the complex to reduce energy cost and reduction in GHG.
- Increased capacity without incorporating additional vessels and valves to lower annual hardware maintenance.
30% Capacity enhancement with minimum investment
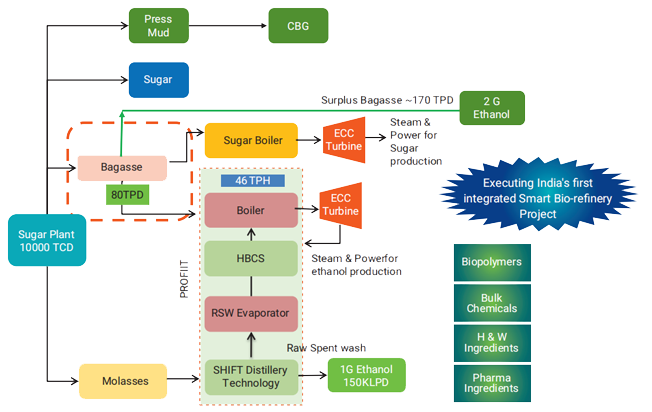
* Typical schematic for 150 KLPD Bio-refinery.
Highlights of technology
- Operator friendly interphase to swiftly switch between existing Ecomol to MaxImolTM mode and vice-versa.
- Lower operational expenditure (OPEX).
- Quick and easy installation enabling immediate turnaround.
- More than 50% of supplied energy can be recovered within the complex to reduce energy cost and reduction in GHG.
- Increased capacity without incorporating additional vessels and valves to lower annual hardware maintenance.